To prevent the static phenomenon of kraft, you need to combine effective grounding techniques, control the environment, and maintain your equipment. Start by installing grounding wires to all conductive parts, guaranteeing they're inspected regularly. Maintain your workshop's temperature between 18℃ and 25℃ with humidity levels between 55% and 75%. Use static eliminators at critical points on your machines and make sure they're regularly cleaned and maintained. Train your staff on the dangers of static electricity and proper practices. This multifaceted approach will greatly reduce risks. If you want to discover more strategies, keep exploring effective solutions for your workplace.
Key Takeaways
- Install and maintain grounding systems for machines and equipment to effectively manage static electricity buildup.
- Control workshop temperature between 18℃ and 25℃ and humidity levels between 55% and 75% to minimize static accumulation.
- Use anti-static clothing for all workers and regularly clean the workspace to reduce dust, which can attract static charges.
- Implement static eliminators at critical points on printing machines and ensure their regular maintenance for optimal performance.
- Provide comprehensive training on static electricity dangers, grounding techniques, and the proper use of static control equipment.
Understanding Static Electricity
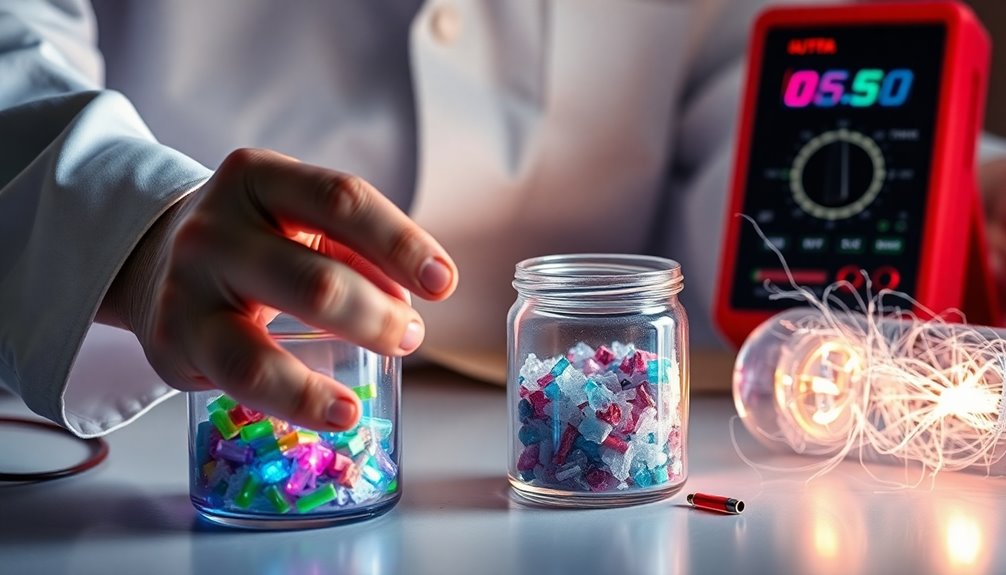
Have you ever wondered why static electricity seems to cling to kraft paper? This phenomenon occurs due to an imbalance of electrical charges between materials, often caused by friction. When you handle or process kraft paper, electrons transfer between surfaces, resulting in static electricity. This build-up can lead to attraction or repulsion between objects, and if the charges discharge, you might even see sparks.
Static electricity is particularly prevalent in dry conditions. In such environments, air acts as an insulator, allowing charges to accumulate on surfaces like kraft paper. The voltage generated can exceed 100 times that of typical electrical outlets, creating a significant risk, especially in areas with flammable materials.
Understanding static electricity is essential for anyone working with kraft paper. It's important for preventing hazards, as static can ignite flammable vapors or damage sensitive electronic components during production and printing processes.
Risks of Static Electricity
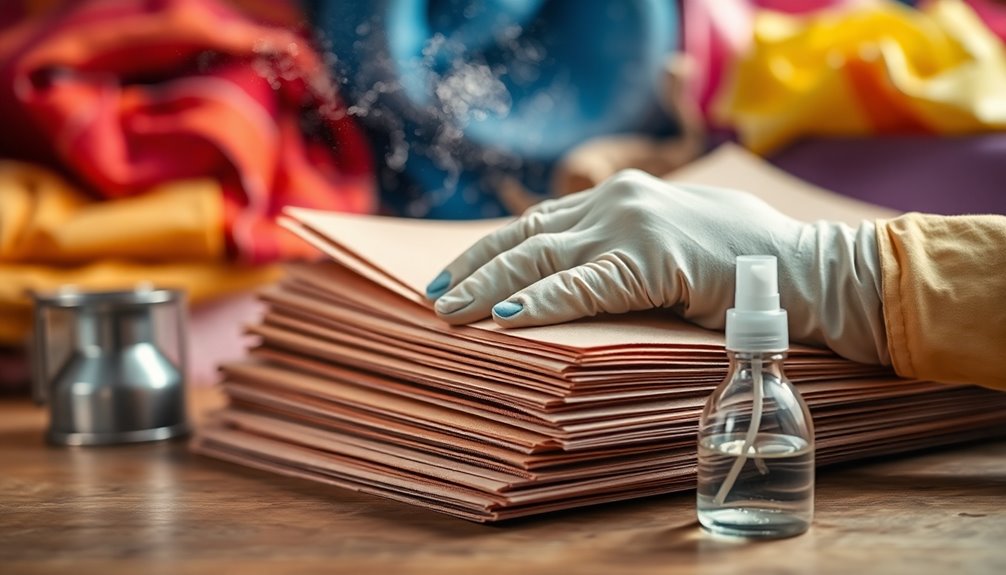
Static electricity poses serious risks in kraft paper production and handling. The presence of static charges can create sparks that ignite flammable substances, especially during printing processes where volatile inks and solvents are frequently used. This ignition risk can lead to catastrophic accidents if proper precautions aren't taken.
Additionally, the accumulation of static electricity can result in electrical shocks, which may injure workers engaged in kraft paper handling or operating machinery. These incidents not only threaten safety but can also disrupt workflow.
Moreover, sensitive electronic devices used in quality control and printing operations are vulnerable to static discharge. A single zap can damage these devices, leading to costly repairs and production delays.
Static electricity also attracts dust and debris, compromising the cleanliness of your production environment. This contamination can negatively impact the quality of your final product.
Lastly, inadequate grounding and bonding practices can exacerbate these static risks. It's essential to implement effective safety protocols to mitigate these hazards and protect both your workers and your equipment.
Effective Grounding Techniques
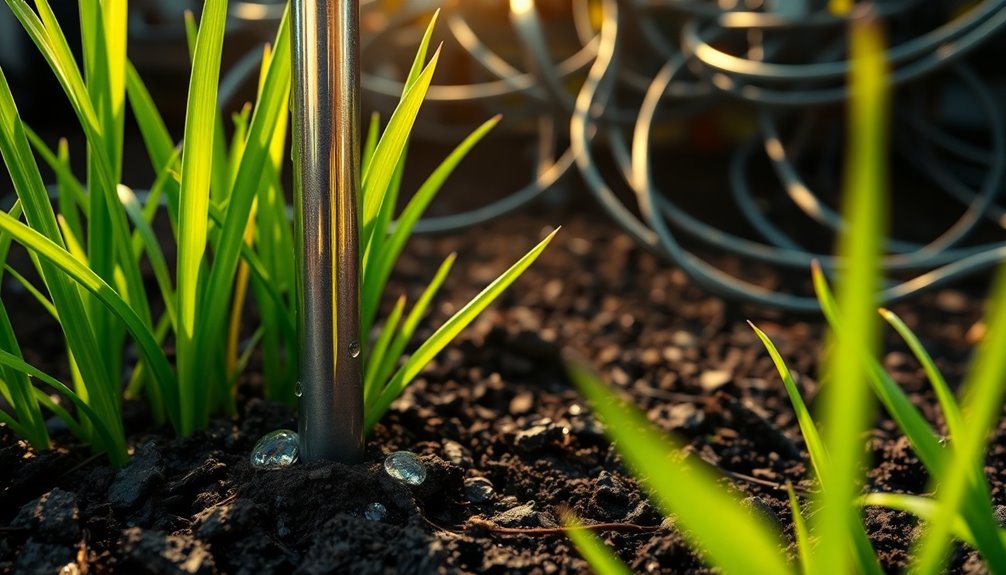
To effectively manage the risks associated with static electricity in kraft paper production, implementing proper grounding techniques is vital. Start by installing a grounding wire for your kraft paper printing machines. This step is essential to reduce static electricity and guarantee safe operation during the printing process.
Don't forget to ground your ink circulation pumps as well; this enhances the overall effectiveness of your static electricity management.
Regularly check and maintain your grounding systems to confirm their functionality and safety. Remember, ineffective grounding can lead to static-related issues that could disrupt your operations.
Additionally, utilizing conductive materials in machine components can greatly improve grounding, decreasing the likelihood of static accumulation during production.
Training your staff on proper grounding procedures and maintenance is equally important. This training guarantees everyone understands the role of effective grounding techniques in sustaining a robust static electricity management system.
Environmental Control Practices
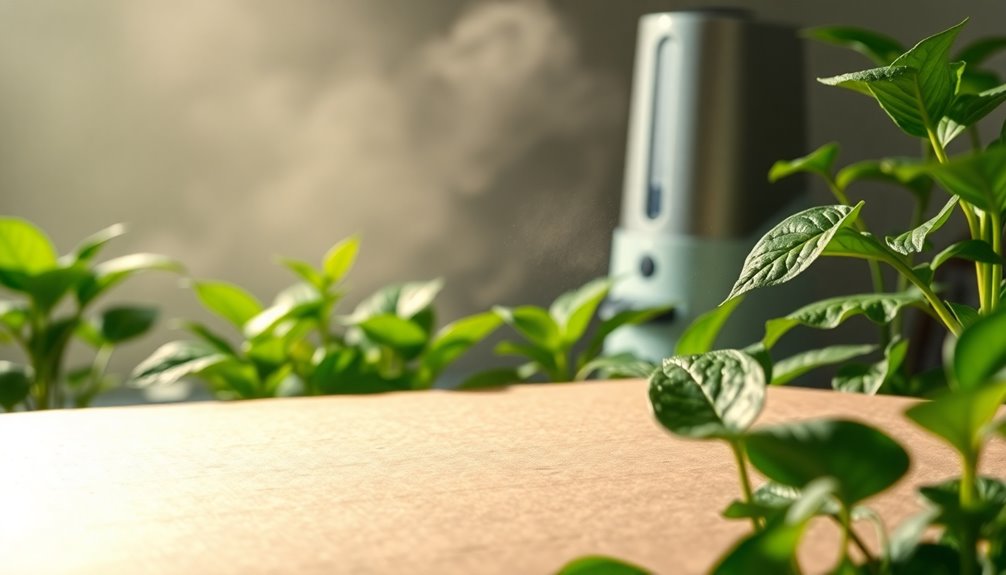
Maintaining the right environmental conditions is essential for minimizing static electricity in kraft paper production. You can achieve this by controlling temperature and humidity levels effectively. Aim to keep the workshop temperature between 18℃ and 25℃. This range optimizes conditions and helps reduce static buildup. Additionally, humidity levels should be maintained between 55% and 75%. Higher humidity can prevent static accumulation, especially since dry conditions can worsen static issues.
Implementing anti-static clothing requirements for all workers is another significant practice. This reduces the risk of static discharge during handling and processing. Regular cleaning of the workshop is also important; it minimizes dust accumulation, which can contribute to static electricity generation on surfaces and materials.
If the environment becomes too dry, consider utilizing water spraying or mopping techniques to increase humidity levels. Here's a quick reference table:
Environmental Factor | Recommended Range |
---|---|
Temperature | 18℃ to 25℃ |
Humidity | 55% to 75% |
Cleanliness | Regular cleaning |
Utilizing Static Eliminators
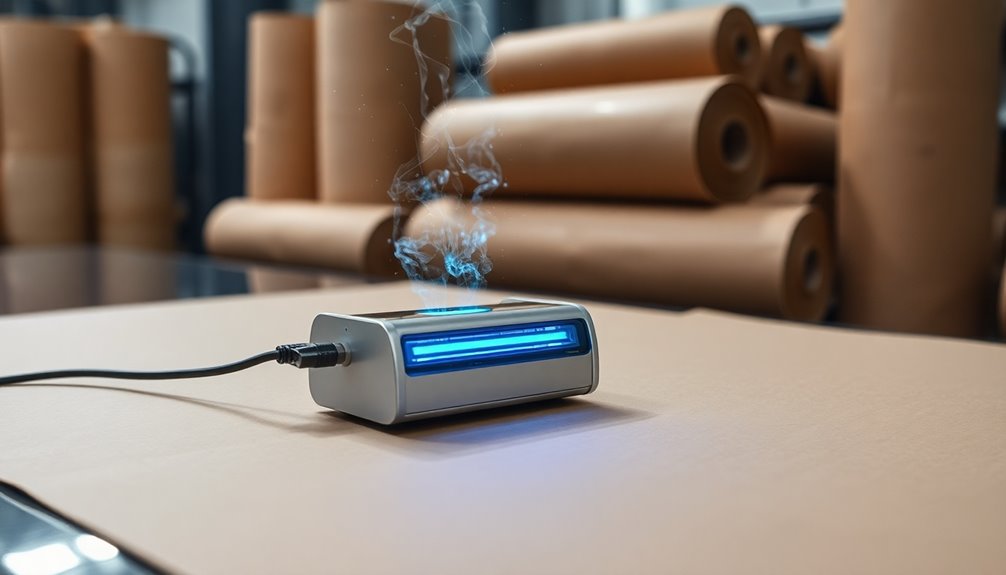
To effectively combat static, you need to strategically install static eliminators at key points on your kraft paper printing machine.
Regular maintenance is just as essential; without it, even the best systems can falter.
Importance of Regular Maintenance
Regular maintenance of static eliminators is vital for keeping your kraft paper production process running smoothly. Even minor malfunctions can lead to increased static build-up, causing disruptions in your workflow. Schedule regular inspections to check for wear and tear, guaranteeing that your static eliminators are correctly positioned to neutralize static charges effectively.
Cleaning your static eliminators is another important step in maintenance. Dust and debris can greatly impede their ability to eliminate static electricity. By keeping these devices clean, you enhance their efficiency and minimize static-related issues.
Additionally, training your staff on the importance of static eliminators and proper maintenance procedures fosters a culture of safety and awareness in your production environment.
Don't forget to maintain a consistent routine for the calibration and function testing of your static eliminators. This proactive approach allows you to identify potential problems early, reducing the risk of production disruptions caused by static electricity.
Strategic Installation Locations
Effective placement of static eliminators is essential for minimizing static electricity throughout the kraft paper production line. You should install static eliminators at critical points, particularly before and after printing. This helps neutralize static charges that can disrupt the printing process.
Positioning them near ink circulation pumps is equally important, as it prevents static build-up that could affect ink flow and quality during production.
In high-static areas, like near cutting and folding machines, utilize multiple static eliminators to guarantee uniform charge distribution. This reduces the likelihood of static-related defects in your final product.
Regularly inspect and maintain these static eliminators, as dirt or wear can considerably diminish their effectiveness.
Make sure your team is trained to recognize potential static accumulation points. Emphasizing the importance of static eliminators in the kraft paper production process enhances overall product quality and safety.
Antistatic Agents and Applications
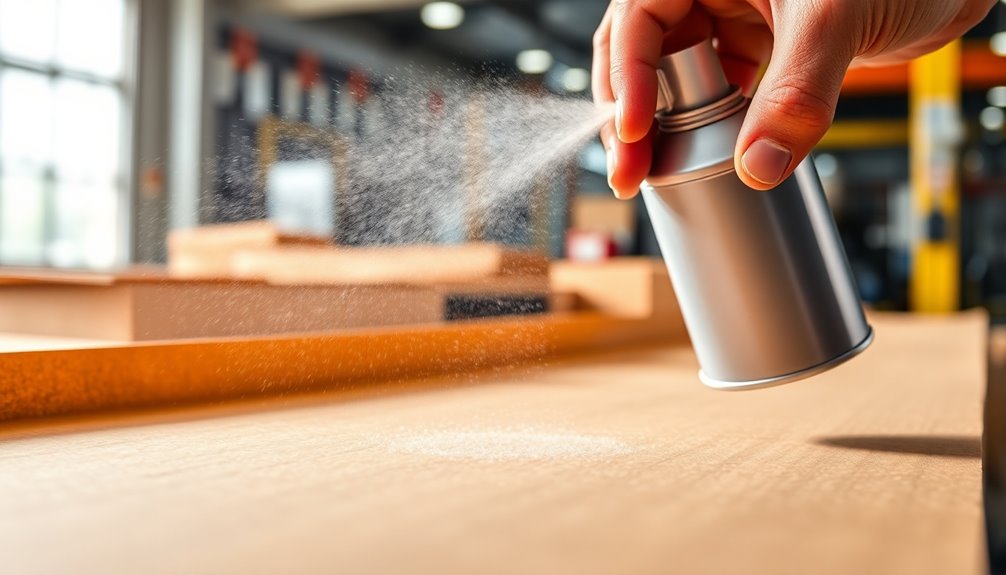
Static electricity can wreak havoc during the kraft paper printing process, making the use of antistatic agents indispensable. You can effectively reduce static electricity levels by incorporating these agents into your ink formulations, especially in high static conditions.
Regularly monitor static electricity levels to determine the appropriate use and dosage of antistatic agents, guaranteeing you achieve ideal results.
When selecting antistatic agents, compatibility is significant. Choose agents that won't adversely affect the ink quality, as this will help maintain consistent printing performance.
Proper application techniques and dosage are essential, so make sure your staff is trained in these areas. This training maximizes the effectiveness of antistatic agents while safeguarding print quality.
The benefits of using antistatic agents extend beyond just minimizing static-related printing issues; they also enhance the overall quality and reliability of your kraft paper products.
Training and Safety Protocols
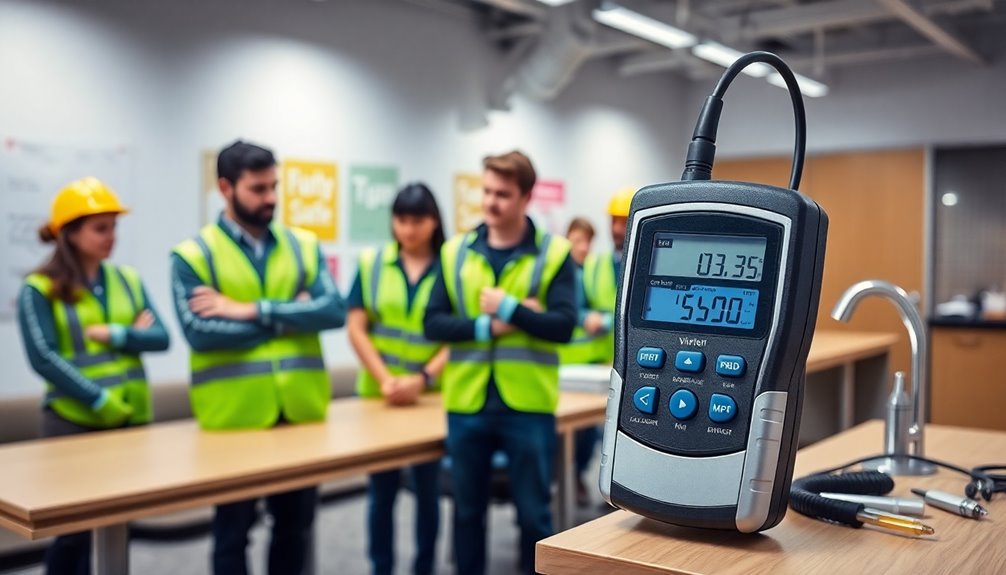
To effectively prevent static issues in your operations, you'll need to focus on grounding procedures training and static safety protocols.
Regular maintenance education will help guarantee that everyone understands their role in minimizing static electricity risks.
Grounding Procedures Training
Proper grounding procedures are vital in preventing static electricity buildup during the kraft paper printing process. To guarantee safety and efficiency, make it a priority to equip all kraft paper printing machines with grounding wires. Regularly inspect these grounding systems to confirm their functionality.
It's essential to train your staff on the importance of proper grounding procedures, highlighting the need to connect all conductive parts of the machinery to a common ground. This connection helps prevent static accumulation.
Implement a routine maintenance schedule to check grounding systems, confirming resistance levels remain below one mega-ohm for effective discharge of static electricity. Don't overlook the grounding of ink circulation pumps; they play a significant role in static control and enhance overall product quality.
During training sessions, incorporate practical demonstrations to illustrate proper bonding techniques and the correct use of grounding equipment. This hands-on approach helps your workers understand how to minimize static risks while handling kraft paper.
Static Safety Protocols
Understanding the risks associated with static electricity is crucial for maintaining a safe working environment in kraft paper production. To effectively manage these risks, you need to implement thorough static safety protocols.
Start by guaranteeing all staff undergo extensive training on the dangers of static electricity. This training should emphasize proper grounding techniques and the use of antistatic agents during production.
Educate your employees on maintaining ideal workshop conditions, keeping humidity levels between 55% and 75% to minimize static buildup. Regular drills and refresher courses are essential; they guarantee every worker can identify potential hazards and respond appropriately to any static-related incidents.
Establish clear guidelines regarding anti-static clothing and equipment. Make it mandatory for workers to wear conductive footwear to reduce static charge accumulation.
Additionally, maintain detailed records of safety inspections and grounding system checks. This documentation not only confirms compliance with static safety protocols but also enhances overall workplace safety.
Regular Maintenance Education
Regular maintenance education is essential for ensuring the safety and efficiency of kraft paper production. You should participate in regular training sessions that focus on grounding techniques, which involve installing grounding wires on printing machines to effectively mitigate static electricity buildup.
Familiarize yourself with the maintenance procedures for static eliminators, as regular inspections and cleaning are key to keeping them operating at peak performance.
Monitoring humidity levels in the workshop is also important. Aim to maintain humidity between 55% and 75%, as this range plays a significant role in preventing static electricity accumulation during production.
Additionally, you'll need to learn how to adjust machine settings based on ink viscosity and flow rates, as these adjustments can control static generation during the printing process.
Implementing a safety protocol is essential, too. Wearing anti-static clothing and using proper grounding methods can greatly reduce the risk of static-related accidents in your working environment.
Frequently Asked Questions
What Materials Are Most Prone to Static Electricity in Kraft Handling?
When handling kraft materials, you'll find that certain materials are more prone to static electricity.
For instance, plastics, rubber, and certain synthetic fibers often generate static charges. Additionally, dry environments can exacerbate the issue, making it essential to take into account humidity levels.
If you're working with kraft paper or films, keep in mind that their surface properties can also influence static buildup.
Being aware of these materials helps in managing static effectively.
How Often Should Grounding Systems Be Inspected for Effectiveness?
You should inspect grounding systems at least once a year to guarantee they're effective.
However, if you notice any unusual static buildup or changes in your environment, it's wise to check them more frequently.
Regular inspections help you identify wear and tear or potential issues before they escalate.
Keeping a close eye on your grounding systems can save you from costly problems down the road, so don't overlook this important maintenance task.
Can Humidity Levels Affect Static Electricity in Kraft Materials?
Yes, humidity levels can definitely affect static electricity in kraft materials.
When humidity is low, static charges build up more easily, leading to increased static electricity.
Conversely, higher humidity can help dissipate these charges since moisture in the air allows for better conductivity.
So, you'll want to monitor humidity levels closely in your environment to manage static electricity effectively.
Keeping conditions balanced can help reduce static-related issues.
What Are the Signs of Inadequate Static Control Measures?
If you're noticing frequent shocks when handling materials, that's a clear sign of inadequate static control measures.
You might find that packaging materials cling together or stick to surfaces unexpectedly.
Additionally, if your equipment shows signs of dust accumulation or if there's an increase in product defects, these are all indicators that static isn't being effectively managed.
Addressing these issues promptly can improve safety and product quality in your operations.
Are There Specific Safety Gear Recommendations for Handling Kraft Materials?
When handling kraft materials, you should wear specific safety gear to protect yourself.
Start with anti-static gloves to minimize static charge transfer. Wear a grounded ESD (electrostatic discharge) wrist strap, especially if you're working with sensitive electronics.
It's also wise to don non-conductive shoes for added safety. If you're in a dusty environment, consider a dust mask, and always use safety goggles to shield your eyes from potential hazards.
Stay safe while you work!
Conclusion
Ultimately, preventing static electricity in kraft processes is essential for safety and efficiency. By understanding the risks, implementing effective grounding techniques, and controlling the environment, you can greatly reduce static buildup. Utilizing static eliminators and applying antistatic agents further enhances your protection. Don't forget to train your team on safety protocols to guarantee everyone's on the same page. With these strategies in place, you'll create a safer, more productive working environment.