Polyethylene film is a versatile material made from ethylene, primarily derived from natural gas and petroleum. It accounts for about 34% of global plastic production, amounting to over 100 million tons each year. You'll find different types, like low-density polyethylene (LDPE) for flexible applications and high-density polyethylene (HDPE) for sturdier uses. This film is widely used in food packaging, agriculture, and retail due to its moisture resistance and lightweight properties. With growing concerns about plastic waste, innovations in sustainability are reshaping how polyethylene is produced and used. Stick around to discover more about its impact and future trends.
Key Takeaways
- Polyethylene film (PE) is a plastic film made from ethylene, widely used in packaging and various industries.
- It comes in different types, including LDPE, HDPE, and LLDPE, each suited for specific applications.
- Common applications include food packaging, agricultural use, healthcare, and retail, providing moisture resistance and customization.
- Polyethylene film is lightweight, recyclable, and can be produced through processes like extrusion and blown film techniques.
- Environmental concerns include its slow biodegradation and impact on wildlife, prompting innovations for more sustainable alternatives.
Definition of Polyethylene Film
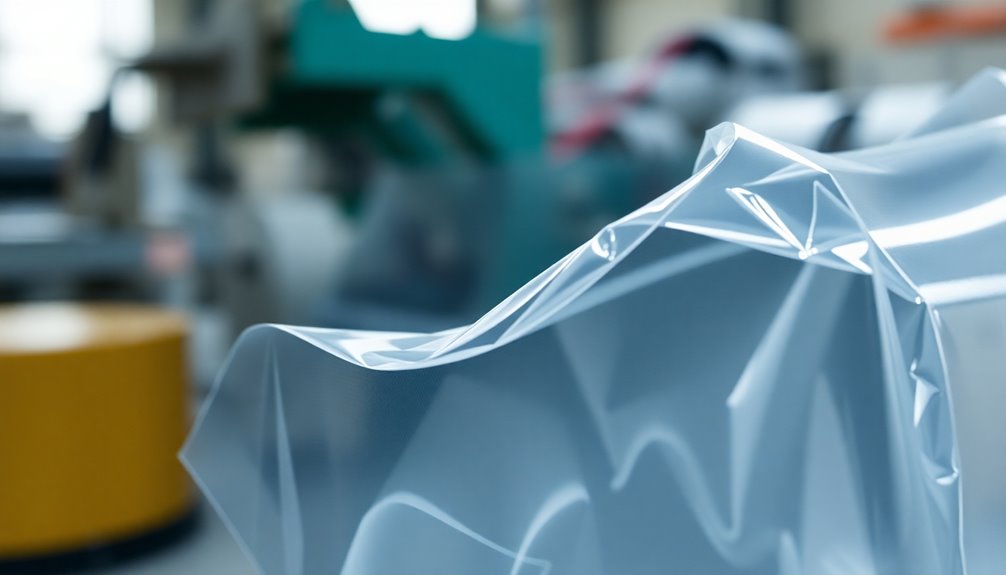
Polyethylene film (PE) is a versatile plastic film made from ethylene, a hydrocarbon sourced from natural gas or petroleum. This plastic film is the most produced globally, with over 100 million tons manufactured each year. It accounts for around 34% of all plastic produced worldwide, highlighting its significance in various industries.
You'll find polyethylene film in different types, such as Low-Density Polyethylene (LDPE), High-Density Polyethylene (HDPE), and Linear Low-Density Polyethylene (LLDPE). Each type has unique properties that cater to specific applications.
Common applications of polyethylene film include packaging materials, agricultural covers, and protective barriers used in construction settings.
The film's excellent moisture resistance, flexibility, and durability make it an ideal choice for both consumer and industrial products. Whether you're wrapping goods for shipping or covering crops, polyethylene film provides reliable protection and performance.
Its adaptability guarantees it meets the diverse needs of various sectors, making this plastic film indispensable in our daily lives. By understanding what polyethylene film is and its applications, you can appreciate its role in modern manufacturing and consumer products.
Types of Polyethylene Film
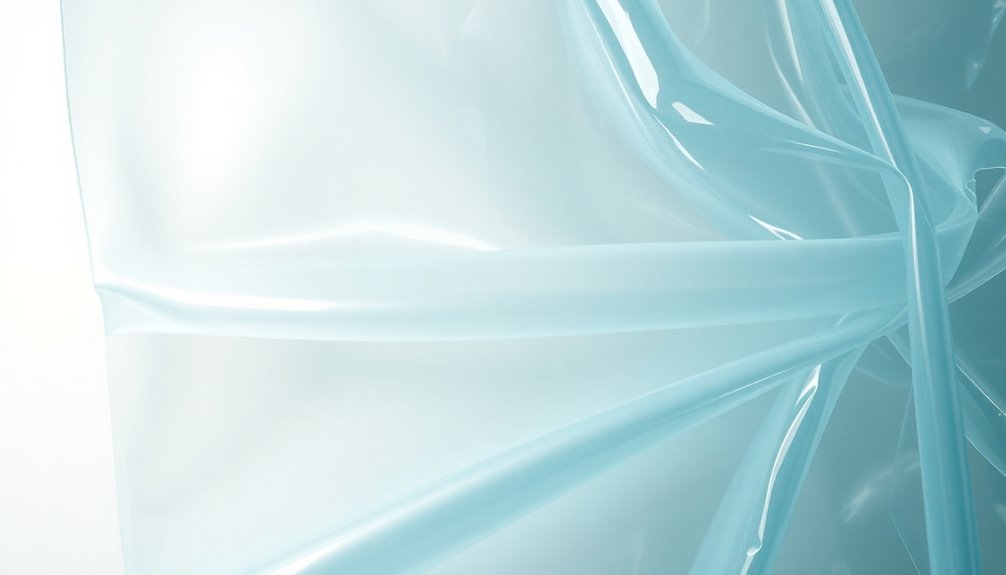
When it comes to the different types of polyethylene film, you'll encounter several variations, each designed for specific uses. Understanding these types helps you choose the right polyethylene film used for your needs.
Type of Polyethylene | Key Characteristics |
---|---|
Low-Density Polyethylene (LDPE) | Flexible, transparent; ideal for shopping bags and food packaging. |
High-Density Polyethylene (HDPE) | Strong, rigid; perfect for products like milk jugs and industrial containers. |
Linear Low-Density Polyethylene (LLDPE) | Combines LDPE and HDPE properties; offers superior tensile strength and impact resistance, often used in stretch films and heavy-duty sacks. |
Additionally, you have Cast Polyethylene, known for its clarity and smooth surface, making it great for packaging films that require high visibility. Blown Polyethylene, on the other hand, is used for thicker, heavy-duty applications, produced via a tubular film process that suits bags and wraps well.
Each type has distinct barrier properties and applications, allowing you to select the best option for your specific requirements.
Applications of Polyethylene Film
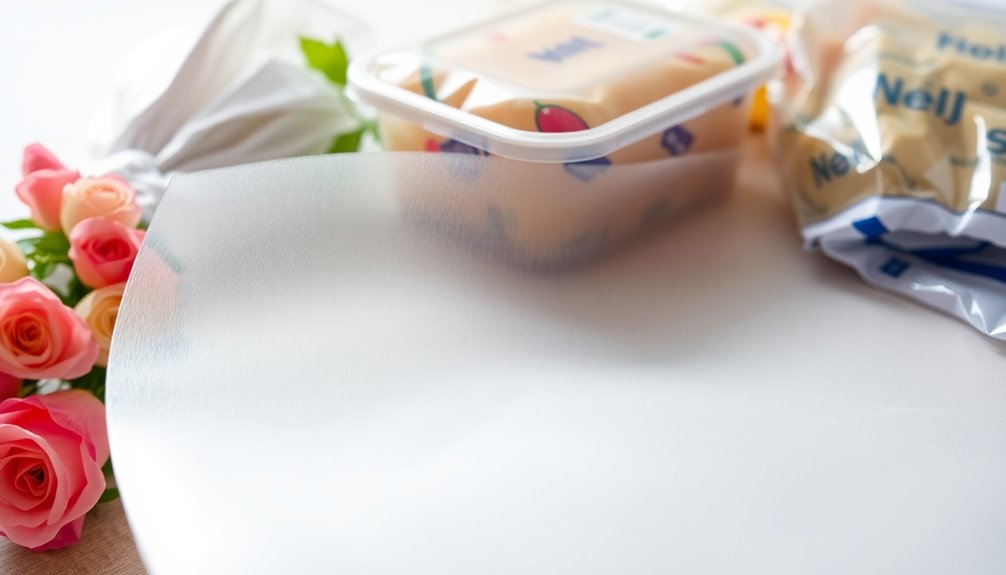
Many industries rely on polyethylene film for its versatility and effectiveness in various applications. In food packaging, it serves as a moisture and contamination barrier that greatly enhances shelf life; in fact, LDPE films comprised 67% of total LDPE use in this sector in 2011.
When it comes to agricultural applications, polyethylene films are indispensable for greenhouse covers and mulch films, helping to increase yields and conserve water, with about 2-3 million tons utilized annually in Europe.
In the industrial sector, polyethylene film offers essential benefits, including protective wraps, pallet covers, and machinery protection, making it crucial for logistics and manufacturing processes.
In healthcare, medical uses of polyethylene film such as sterilization wraps and disposable gowns are necessary for maintaining hygiene and safety standards.
Finally, retail applications showcase polyethylene film's versatility and cost-effectiveness, as it's commonly used for shopping bags and product wraps, catering to a variety of consumer goods.
Polyethylene in Labeling
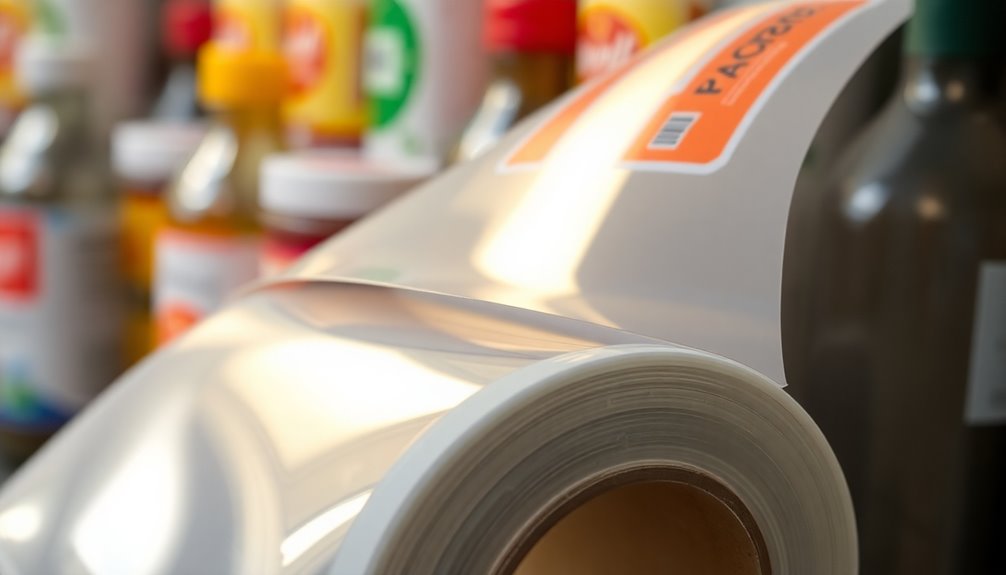
Utilizing polyethylene in labeling has become standard due to its cost-effectiveness and versatility. It's the most commonly used plastic in label manufacturing, accounting for a significant portion of the labeling market.
You'll find that polyethylene labels boast excellent durability and resistance to moisture and chemicals, making them an ideal choice for both consumer and industrial applications.
One of the standout features of polyethylene labels is their customization options. You can choose from different colours, shapes, sizes, and adhesive types to meet your specific labeling needs.
Whether you're labeling products in a retail setting or creating industrial labels for tough environments, polyethylene's strong and flexible nature allows for effective adhesion on various surfaces, including squeezable containers.
Moreover, polyethylene labels are recyclable, which means you can contribute to sustainability efforts while ensuring high-quality performance.
By opting for polyethylene in your labeling projects, you're not just choosing a reliable material; you're also making a smart, environmentally friendly decision.
Environmental Impact of Polyethylene
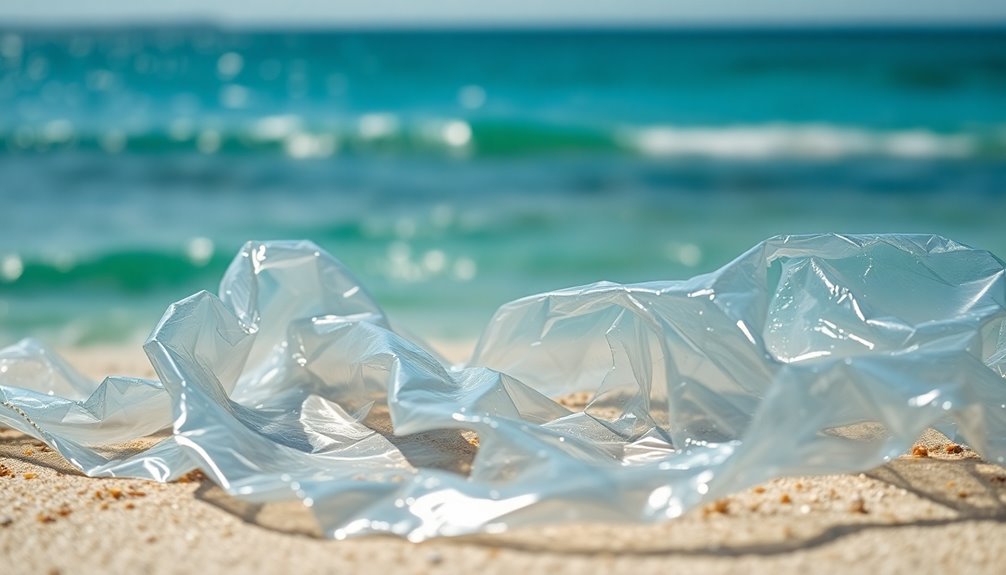
When you consider the environmental impact of polyethylene, the challenges of biodegradation stand out.
With billions of plastic bags produced every year and only a small fraction recycled, it's clear that addressing waste is vital.
Recycling initiatives and innovations are essential to reduce this burden and promote a more sustainable future.
Biodegradation Challenges
Polyethylene film poses significant biodegradation challenges that contribute to the growing plastic pollution crisis. It can take decades to biodegrade in natural environments, leading to severe environmental pollution.
In the U.S., around 380 billion plastic bags are produced each year, with only about 5% recycled. This leaves a staggering amount of plastic waste to clutter landfills, rivers, and oceans, harming wildlife and disrupting ecosystems.
The slow biodegradation of polyethylene poses substantial risks; animals often ingest plastic debris or become entangled in it, causing injury or death.
Fortunately, there are innovations aimed at addressing these issues. Researchers are exploring ways to modify the carbon chain and incorporate additives that can accelerate the biodegradation process, enhancing the environmental impact of polyethylene products.
Additionally, efforts to develop biodegradable alternatives, such as starch-based films, are underway. These alternatives could effectively mitigate the long-term environmental challenges posed by traditional polyethylene materials.
Recycling Initiatives
Addressing the challenges of polyethylene film biodegradation requires a strong focus on recycling initiatives. With around 380 billion plastic bags produced annually in the U.S. and only about 5% recycled, the urgency for better recycling programs couldn't be clearer.
Polyethylene film can take decades to biodegrade, amplifying the need to tackle the environmental impact of plastic waste effectively.
Recycling polyethylene films involves specialized processes due to their lightweight and flexible nature, complicating traditional methods. However, there's promising progress in developing dedicated recycling programs and infrastructure specifically for this type of plastic. These initiatives aim to increase recycling rates and reduce plastic waste in landfills.
Innovative approaches are also being explored, including additives that enhance biodegradability and the creation of biodegradable alternatives.
By supporting these recycling initiatives, you can play a crucial role in minimizing the environmental impact of polyethylene film. It's important to stay informed and participate in local recycling efforts, ensuring that polyethylene film is disposed of responsibly.
Together, we can work towards a more sustainable future while addressing the pressing challenges of plastic waste.
Benefits for Packaging

Choosing polyethylene film for packaging offers numerous benefits that appeal to various industries. Its versatility and cost-effectiveness make it a popular choice. Here are three key advantages:
- Moisture Resistance: Polyethylene film protects your products from moisture and chemical contaminants, extending shelf life and ensuring quality.
- Lightweight: The lightweight nature of polyethylene film helps reduce shipping costs and minimizes environmental impact, contributing to a lower carbon footprint during transportation.
- Customizable: You can tailor polyethylene film in thickness, color, and design to meet specific packaging needs, enhancing brand visibility and appeal.
Moreover, the recyclability of polyethylene film supports sustainable packaging practices. By being able to process and reuse this material, you can greatly reduce overall plastic waste.
This is especially important in an era focused on environmentally friendly solutions. Additionally, using polyethylene film can even improve the efficiency of transporting goods like natural gas by maintaining product integrity.
With all these benefits, it's clear why polyethylene film is a top choice for packaging across various sectors. Embracing it not only enhances your packaging strategy but also contributes to a more sustainable future.
Production Processes of Polyethylene Film
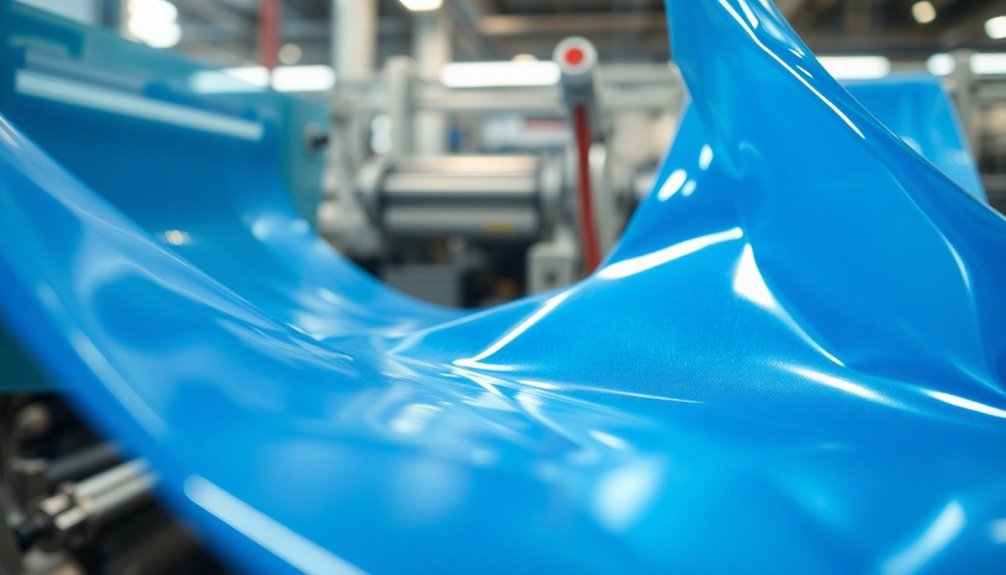
When you explore the production processes of polyethylene film, you'll find that extrusion techniques play a vital role in shaping the material.
The blown film process creates tubular films by introducing air into molten plastic, while casting methods offer clarity and a smooth surface.
Understanding these techniques helps you appreciate the versatility and quality of polyethylene films in various applications.
Extrusion Techniques
Producing polyethylene film primarily involves extrusion, a process where plastic pellets are melted and forced through a die to create a continuous sheet.
There are several extrusion techniques you should know about:
- Blown Film Extrusion: This method creates tubular films by blowing air into the molten polyethylene, resulting in lightweight and flexible films perfect for packaging.
- Casting: In this technique, melted polyethylene is poured onto a flat surface and cooled, which leads to films with higher clarity and smoothness compared to blown methods.
- Co-Extrusion: This advanced technique layers different types of polyethylene, enhancing the films' properties, such as barrier performance and strength, by combining materials with varying characteristics.
The production of polyethylene films usually takes place in high-temperature and high-pressure reactors, where controlled polymerization conditions dictate the branching and density of the final product.
Blown Film Process
The blown film process is a crucial method for creating polyethylene films that are lightweight yet strong. In this process, molten polyethylene is extruded through a circular die and inflated into a tubular film by blowing air into it, forming a bubble shape. This technique allows you to produce thin films with uniform thickness and excellent mechanical properties, making them ideal for various applications, such as packaging and agricultural films.
One of the key advantages of the blown film process is its ability to incorporate multiple layers through co-extrusion. This enhances the film's barrier properties and functionality, catering to specific needs. The typical thickness range for blown polyethylene films is between 0.5 to 10 mils, which can be adjusted based on your application requirements.
Here's a quick overview of the blown film process:
Aspect | Details | Importance |
---|---|---|
Mechanical Properties | Strong and flexible | Ideal for diverse applications |
Co-Extrusion | Multi-layer films | Enhanced barrier properties |
Thickness Range | 0.5 to 10 mils | Versatility for various uses |
Cooling occurs as the film is drawn upward and flattened, solidifying it for durability.
Casting Methods
Casting methods for polyethylene film offer a highly efficient way to create thin films with exceptional clarity and uniformity. This production process involves pouring molten polyethylene onto a flat surface, allowing you to control film thickness and achieve a smooth surface.
Cast polyethylene films are particularly known for their optical quality, making them perfect for packaging food products and display items.
Here are three key benefits of the casting method:
- Energy Efficiency: The casting process generally requires less energy compared to blown film extrusion, making it a more cost-effective option.
- Additive Incorporation: You can easily incorporate various additives during production, enhancing properties like UV resistance, moisture barriers, and anti-static features.
- Clarity and Smoothness: Cast films exhibit superior clarity, ideal for applications where visual appearance is essential.
However, it's significant to recognize that cast films typically have lower tear resistance than blown films due to the lack of orientation during production.
This could limit their suitability for certain applications where durability is a priority. Overall, the casting method remains a popular choice for producing high-quality polyethylene film.
Comparison of Film Types
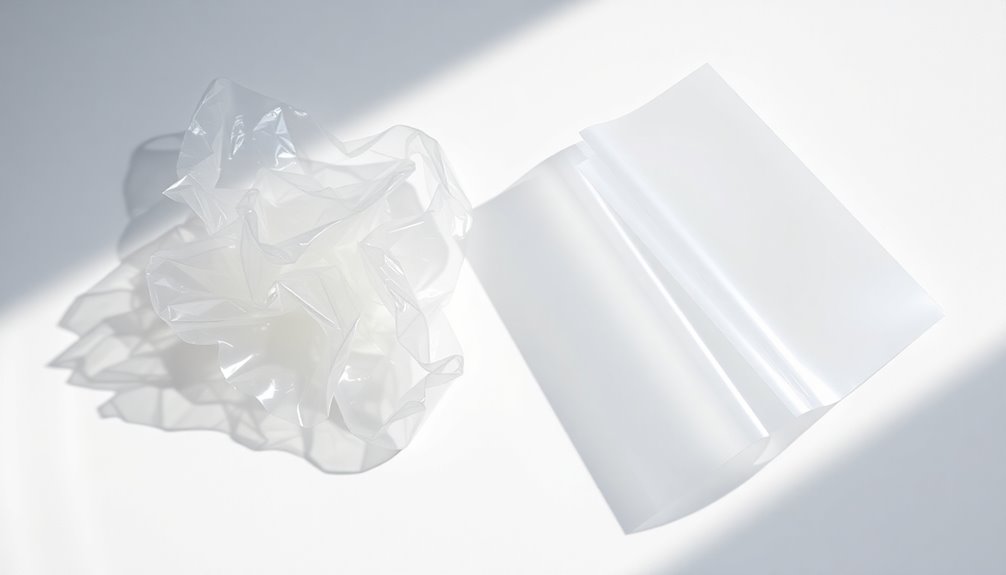
When considering various types of polyethylene film, it is essential to understand their distinct properties and applications. Each type of polyethylene film has unique characteristics that make it suitable for different uses.
Film Type | Key Properties |
---|---|
LDPE | Density: 0.910–0.940 g/cm³; flexible, ideal for bags and food packaging. |
HDPE | Density: 0.940–0.970 g/cm³; tough, low gas permeability, great for rigid packaging like milk containers. |
LLDPE | Density: 0.916–0.940 g/cm³; superior tensile and impact strength, used for stretch films and heavy-duty sacks. |
Metallocene Polymers | Modulate properties like strength and flexibility through specific processes. |
Ethylene Copolymers | Enhance flexibility and adhesion, suitable for specialized applications. |
Low-Density Polyethylene (LDPE) is known for its flexibility, making it perfect for lightweight applications. On the other hand, High-Density Polyethylene (HDPE) excels in strength, making it ideal for more durable products. Linear Low-Density Polyethylene (LLDPE) combines flexibility with enhanced tensile and impact strength, making it a favorite for stretch films. Understanding these differences helps you choose the right film made from ethylene for your specific needs.
Innovations in Sustainability
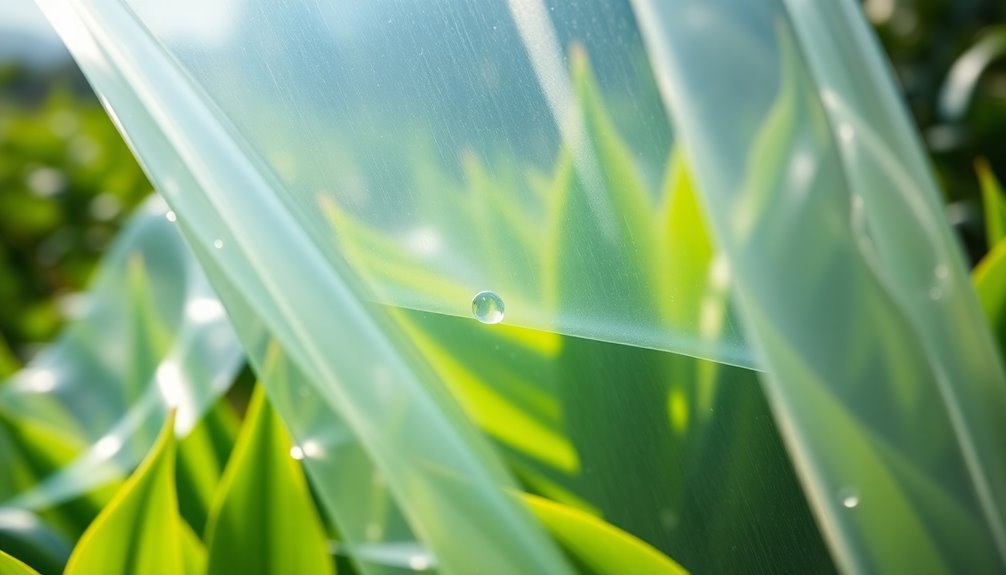
As the push for sustainable practices intensifies, innovations in polyethylene film are stepping up to address environmental concerns. You'll find several promising advancements that aim to reduce the environmental impact of plastic waste while maintaining functionality.
- Biodegradable Additives: These additives enhance the degradation process of polyethylene films, making them more eco-friendly by breaking down faster in the environment.
- Recycled Polyethylene: The use of recycled materials in film production has surged, thanks to technology that allows for a higher percentage of post-consumer content. This reduces reliance on virgin materials and promotes a circular economy.
- Multilayer Films: New co-extrusion techniques enable the creation of multilayer films that combine different polymers. This optimizes barrier properties, minimizes material usage, and improves mechanical properties, all essential for sustainability.
Additionally, the exploration of bio-based polyethylene alternatives, like starch-based options, offers a more environmentally friendly choice.
These innovations not only enhance the performance of polyethylene films but also pave the way for a greener future, demonstrating that sustainability and functionality can go hand in hand.
Future Trends in Polyethylene Film
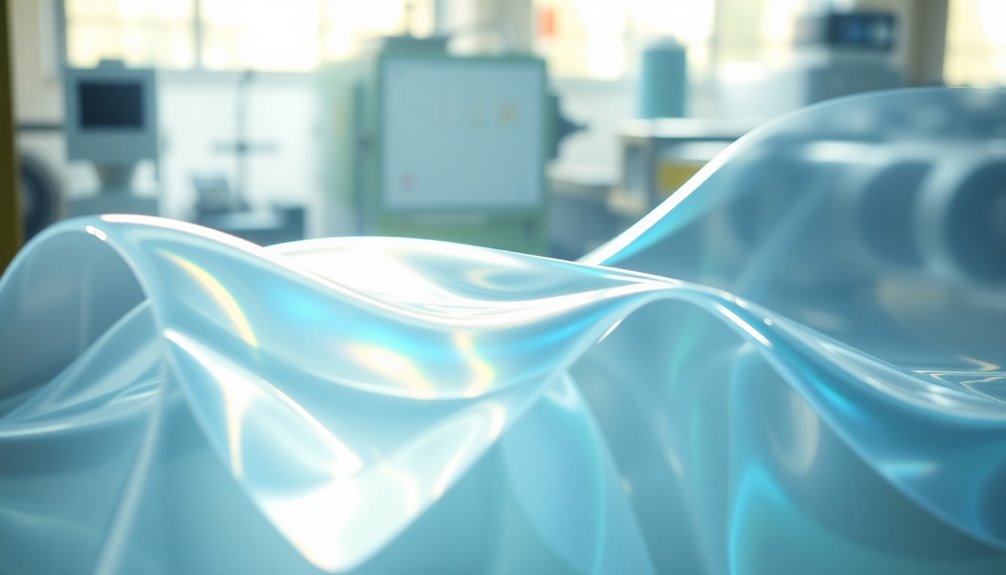
The future of polyethylene film is shaping up to be more innovative and sustainable, driven by consumer demand for eco-friendly solutions.
You'll see a significant rise in biodegradable polyethylene films as businesses prioritize sustainability and environmental responsibility. Innovations in production processes, like the development of metallocene polymers, enhance the strength and flexibility of polyethylene films, making them suitable for a wider range of applications.
Incorporating smart technologies, such as sensors embedded in the films, could transform how you monitor product conditions in real time, revolutionizing packaging and supply chain management.
As recycling technologies advance, the recyclability of polyethylene films will improve, potentially boosting the current recycling rate of just 5% for plastic bags in the U.S.
With global regulations on plastic tightening, the industry is also focused on developing alternative materials that maintain performance while minimizing environmental impact.
You'll find that these trends not only benefit the planet but also cater to your growing awareness of sustainability in packaging and products. Embracing these changes guarantees a future where polyethylene films contribute positively to the environment.
Frequently Asked Questions
What Is Polyethylene Film Used For?
You'll find polyethylene film used in various ways that enhance protection and efficiency.
It's great for packaging, keeping moisture and contaminants at bay, which helps preserve products.
In construction, you can use it to cover surfaces and equipment, preventing damage.
It's also beneficial in agriculture for greenhouse covers and mulch, boosting crop yields.
Plus, you'll notice it in medical settings, ensuring hygiene with items like sterilization wraps and disposable gowns.
Is Polyethylene Film Waterproof?
Yes, polyethylene film is waterproof due to its low water vapor permeability.
This makes it an effective barrier against moisture, which is why you often see it used in packaging to protect products.
If you're considering agricultural applications, its waterproof properties are great for greenhouse covers and mulch films, helping to maintain moisture control for plant health.
Just remember, prolonged exposure to harsh conditions can affect its durability.
Is Polyethylene the Same as Plastic?
You might wonder if polyethylene is the same as plastic. While polyethylene is indeed a type of plastic, not all plastics fall under its category.
Plastics are a broad range of synthetic materials, and polyethylene specifically refers to a popular form made from ethylene. It's used in various products, but it's important to recognize that plastics include many other materials, like polystyrene and polypropylene, which have different properties and applications.
Where Is Polyethylene Film Used?
You'll find polyethylene film used in various industries.
It's commonly employed in packaging, providing flexibility and moisture resistance for products.
In agriculture, you'll see it as greenhouse covers, boosting crop yields.
The construction sector uses it as vapor retarders to manage moisture.
Additionally, in food packaging, it extends shelf life by acting as a barrier against contaminants.
This versatile film is essential in protecting machinery and surfaces during storage and transportation, too.
Conclusion
In conclusion, polyethylene film's versatility makes it essential across various industries, from packaging to labeling. While its environmental impact raises concerns, innovations in sustainability are paving the way for a greener future. By staying informed about the different types and applications of polyethylene film, you can make more sustainable choices in your projects. As the industry evolves, keeping an eye on future trends will help you adapt and embrace more eco-friendly alternatives.